Common Challenges For Cold Storage And Solutions
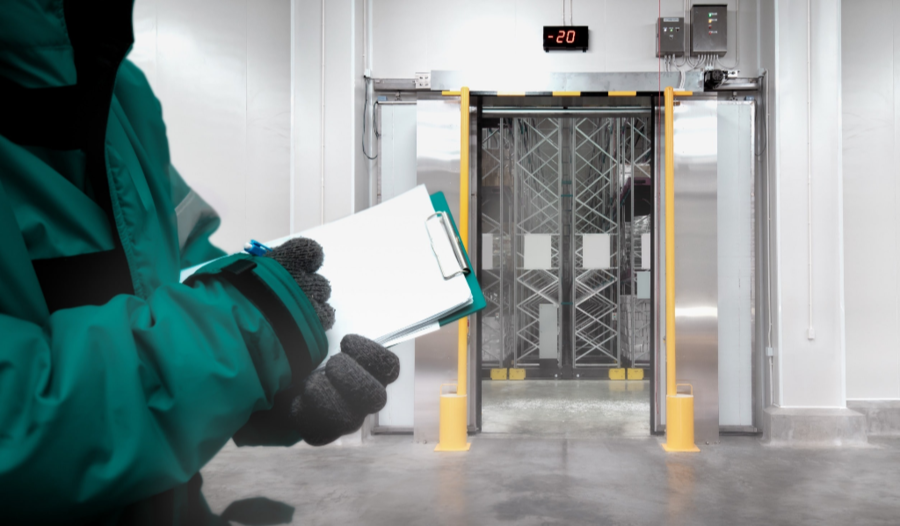
When it comes to bulk handling temperature-sensitive perishable goods between production and marketing, cold storage is one of the top choices for stakeholders. As with rapid ongoing urbanisation, an increase in the level of consumption of various products and goods is happening in sectors like the food industry, biotechnology, pharmaceuticals, and medical fields. And the perishability of the product is what pushed the demand for cold storage.
With this, efficient and effective cold chain management has become more crucial. It requires strategic planning and organisational skills because many significant causes of concern are involved in managing a cold storage warehouse.
Six of the most common cold storage challenges
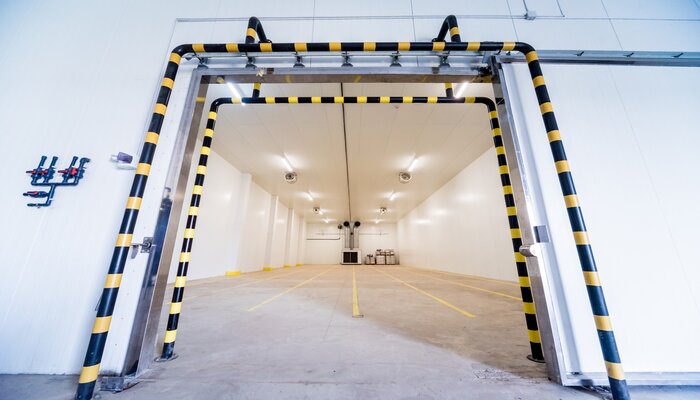
If not addressed right, the standard set of challenges that the cold chain industry often deals with can have serious consequences. The following are some common challenges a cold storage warehouse might have.
1.Temperature and humidity regulation
Sometimes, chilling larger areas is less efficient than the smaller ones. But cold storage facilities, including high-density storage, are often designed to maximise capacity. So, a heat exchange occurs in the temperature-controlled areas whenever a door is opened. Or, every time a product is removed from a freezer, it heats up. As it is returned to the freezer, this might slightly raise the temperature affecting product quality because moisture build-up due to temperature changes can happen. Seasonal temperature changes also influence the internal quality environment, increasing the risk of product spoilage.
2.Power consumption
Providing cold storage services consumes an enormous amount of electricity as it allows for a 24-hour operating facility. Also, as energy cost is increasing consistently, the challenge of keeping the power consumption costs as low as possible adds a big concern. Because to maintain stable temperatures and protect the inventory of frozen goods, massive amounts of energy are needed to run refrigeration equipment nearly nonstop. The bigger the square footage, the higher the power consumption.
3.Product and warehouse rack label challenges
For racking and product, it needs utterly different label requirements than the normally used one. Unique temperature-resistant material must be implemented because the cold temperature affects the performance of the substrate, adhesive and ink. If the poorly constructed labels quickly curl, crack or encounter frost build-up, it can result in unidentified products, leading to a failed scene. So, to address these cold storage challenges, the facilities require reliable barcode labels to support the cold storage environment. Another challenging factor is choosing between magnet or adhesive-backed labels depending on various cold storage warehouse conditions.
4.Customised facility for various product categories
Another significant challenge faced in a cold storage facility is fulfilling the diverse needs of cold storage customers. Depending on the type of products, different areas of the same warehouse need to be kept at different temperatures. No doubt, tomatoes require different conditions compared to ice cream. For example, when fresh produce needs to be held at 55 degrees F, meat must be stored at 28 degrees F, and ice cream should be kept at -10 degrees F. All these bring operational complexity in ensuring a high level of customisation of facilities to store specific items.
5.Product traceability
Accurate knowledge of product location (in warehouse rack or in transit) is a critical part of cold storage warehouse operations. Every pallet in the warehouse needs to be traced depending on its expiry date, freezing temperature, and freezing date, along with specific rules and regulations (if they have any). Because some products, like fresh produce, might require additional control of variables like humidity or carbon dioxide where accurate documentation is needed. So, adopting all the inventory traceability features across all the inventory transactions is another big challenge.
6.Keeping workers safe and productive
Then, there's the human factor as well. The cold storage industry needs to deal with labour and productivity issues. Workers in cold storage facilities need to bundle up to keep warm. Because the workers performing cleaning, maintenance, and machine operations are permanently exposed to multiple types of risks, including cold-related illnesses like flu, influenza or bronchitis, many occupational accidents can also happen. So warehouses need to arrange specialised equipment and protective wear like goggles, gloves and appropriate clothes to take some frustration and discomfort out of a worker's routine.
Some key solutions to help you run your facility
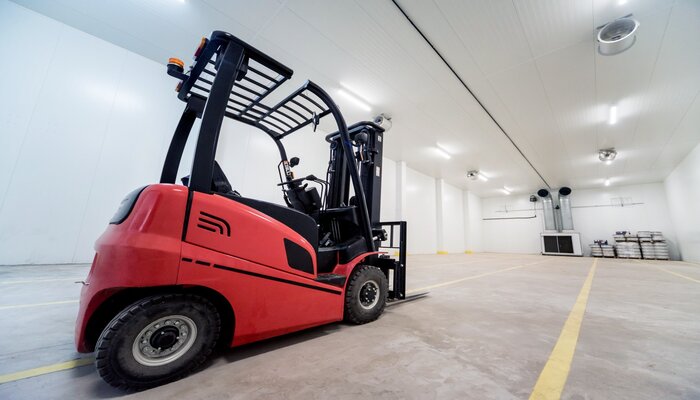
Following are some of the critical solutions that you can employ to manage your cold storage units efficiently.
Maintain temperature ranges and specific solutions
As cold room services don't just hold one type of product, you will have a specific unit for each product, and temperature should be regulated in each part of the cold storage unit. For example, you can create barriers between different temperature zones by installing a modular insulated wall system to divide each temperature zone. These plastic modular curtains are more like shower curtains that can be deployed and redeployed to separate warehouses into different temperature zones.
Adopt technology and employ automation
Adopting technology, including automated storage and retrieval systems, advanced refrigeration systems, and energy-efficient cooling technology, can improve the efficiency of cold storage. To make better use of space and labour, employ automation wherever possible. Implementing automation can help you keep energy costs down by eliminating the possibility of human error, as it minimises the need for human labour. Such as using automated palletisers and depalletisers can enable you to operate with very few employees, reducing loading and unloading times.
Maintain up-to-date records
As products kept in a cold warehouse are sensitive to temperature change, you must keep track of your every inventory. You can use temperature sensors to keep a precise record of the temperature details, trigger alarms and spot potential lapses. Modern software will also allow you to scan pallets and give you accurate records in your computer database.
Use the right equipment
You need to have modified equipment and tools for different controlled options in your cold storage facility, like computers, forklifts, sensors, or scanners. Provide workers with personal protective equipment like insulated coats, pants, and gloves. Your cold storage warehouse equipment should be designed with buttons that are large enough to be felt through work gloves. The steel of industrial racking must be prepared to work at extreme temperatures. And you must focus on using batteries with larger voltages.
Maintaining cold storage warehousing is definitely a priority
In a cold storage service, when the extreme cold might affect employees' health or consume more power, frequent maintenance of cold chain storage facilities can yield many benefits in no time. From prolonging shelf-life to temperature control to reducing spoilage, cold storage warehousing has many significant advantages. Even not just store perishable goods for some time, companies providing cold room services near you like Zion Fresh also offers logistics facilities.